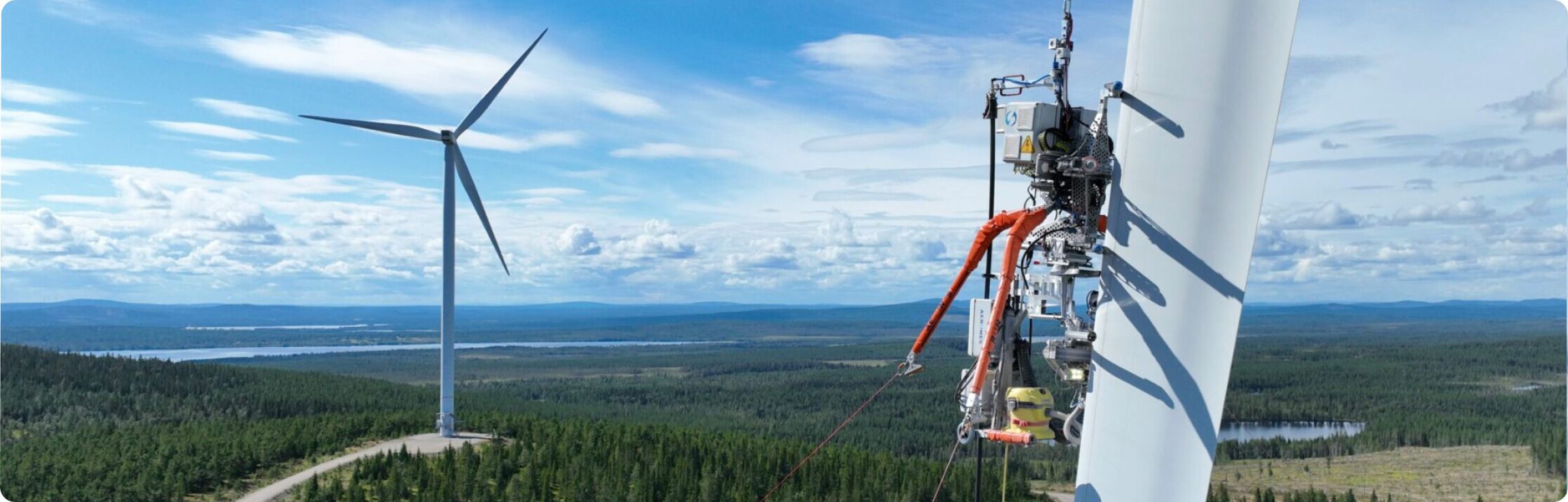
Streamlining Aerones' high-altitude compliance workflow with Next Matter
Aerones is an innovative tech company based in Riga that is revolutionising wind turbine maintenance. They have a dedicated team of over 240 professionals across Europe and offer a range of services including robot-assisted inspections, cleaning, coating, and repair for wind turbine blades. By focusing on intelligent predictive maintenance, Aerones aims to improve wind asset management and reduce downtime, costs, and carbon footprint. Their cutting-edge drones and inspection technology allow for efficient planning and effective repair strategies, ultimately contributing to the accessibility and sustainability of renewable energy.
‍
The Challenge
Although their manual processes had established a strong foundation and good client relationships, the increase in success also brought about an increase in workload. Aerones was faced with the operational challenge of having to utilise inefficient methods such as paperwork and Google Drive. A lack of a systematic approach to capturing and reporting information, which are crucial to their Health & Safety workflows as well as their Quality Management workflows posed a potential problem as they grew. Their team knew efficiency was particularly critical in areas like compliance with internal policies, quality standards, and regulations, and that there was an opportunity to improve in these areas.
‍
Consistency and accuracy
As they continued to increase their ground-team size and gain new business, having a manual and partially paper-based workflow made it difficult to maintain consistency and accuracy, increasing the risk of human error and potentially compromising safety standards. It simply wasn’t sustainable and stood at odds with their ambition to scale and continually improve their processes.
‍
Streamlining client communication
Moreover, the necessity of keeping clients informed about compliance and safety progress could hinder their growth if not streamlined into an efficient and effective process. Maintaining a manual workflow had worked well at Aerones in their earlier stages of growth, but as their ambitions and clientele increased, so too would the workload to a volume that could not be sustained without automation.
‍
Future scalability
The Aerones team recognized that in the future as the volume of work scaled, they would need reliable, automated workflows in order to keep up with the workload and maintain speed and accuracy. Crucially, their workflows needed to be designed to handle operations at scale without breaking.
‍
Automation as the solution
Automation was the most innovative option for them. By being prescriptive with workflows that would run automatically and consistently, they aimed to ensure that their Safety and Quality Managers, like Lilija, would no longer have to worry about the proper and consistent execution of reporting. They wanted to free managers from the growing labor of administrative worries, and enable them to focus on their true jobs: root-cause analysis and service improvement.
‍
If our processes are not accurate and information is missed in reporting from our field operatives or anywhere else in the information chain, there could be a dangerous accident. So getting our compliance and near-miss reporting to be seamless, reliable and easy for all operatives to use is critical to the safety of our people and our delivery of services to our clients.

‍
Lilija Breiva, Health, Safety and Quality Manager at Aerones
‍
‍
The Solution: Next Matter
To address these challenges, Aerones made a strategic decision to leverage Next Matter, a workflow automation solution known for its exceptional compliance capabilities. By implementing Next Matter, Aerones redefined their internal processes and established well-defined Near-Miss and Job Safety Analysis workflows that optimise efficiency and ensure compliance and information completeness from all stakeholders, while also making the entire process more easily manageable for their in-house team.
‍
Using Next Matter, Aerones has successfully implemented more than five workflows, empowering their employees to report using external links and providing them with a user-friendly interface. This streamlined approach has allowed for seamless collaboration and efficient data management between operatives working on the ground across Europe, and their in-house team in Riga, ensuring that all necessary steps are always followed and leaving no room for missing elements.
‍
With Next Matter, Lilija says she has a better control, an easy way of updating and implementing processes, better oversight of all their operatives, safety processes and compliance and near-miss reports coming in, making them easier to manage as a one-person team.
‍
I’ve also built these processes myself so I can make any changes without any technical support. I think it's great that you can build it, then can quickly update it whenever you need to.
I really like Next Matter. I like it because it's very simple.

‍
Lilija Breiva, Health, Safety and Quality Manager at Aerones
‍
‍
.jpg)
The Results
We have implemented 5 workflows now, one of them is our Near-Miss workflow. It’s easily externally available for technicians and all our employees via QR code. It’s easy for them to use without training, because all the steps are in order.
It’s now impossible for any information to be missed with all the required steps built in. Some steps are automated making it easier and quicker for me to manage accurately. It’s simple, fast and we can rely on it to receive all required information.

‍Lilija Breiva, Health, Safety and Quality Manager at Aerones
‍
With streamlined data reporting and prompt action based on received information, Aerones continues to effectively meet both internal and client requirements as established by governmental bodies as well as the clients themselves. The move to Next Matter’s no-code workflow automation has not only bolstered Aerones’ performance and reputation in the renewable energy sector but also strengthened client relationships through accurate, rapid and efficient responses to emerging issues.
‍
I don't think about reports, they are automated so I can focus on investigation processes now.

‍Lilija Breiva, Health, Safety and Quality Manager at Aerones
‍
Moreover, the implementation of Next Matter has empowered Aerones to allocate more time and effort towards investigative tasks. This has contributed to their overall efficiency and productivity, allowing them to delve deeper into research and development. With a well-structured and automated workflow in place, Aerones can now focus on driving innovation and pushing the boundaries of technology for the benefit of the renewable energy sector, propelling their company and clean energy generation towards new heights.
Challenges:
Aerones encountered workflow scalability challenges as they grew. Their manual processes and client relationships were strong, and growing success increased their workload. To maintain efficiency, minimize errors, optimize scaling, and deliver world-class service, they recognized the need for a streamlined workflow.
‍
Results:
Aerones improved quality management, reduced compliance risk, and streamlined collaboration. Their automated Near-Miss workflow can be updated without disrupting live processes when policies change, ensuring uninterrupted operations and complete information input at every step.